Reaction Injection Molding Innovations in Clinical Equipment
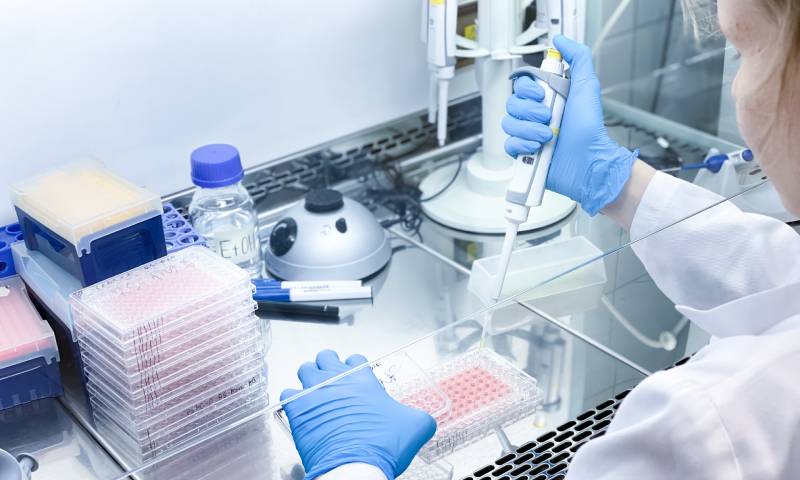
Medical manufacturing for clinical equipment employs innovative techniques, such as reaction injection molding (RIM). It’s a perfect example of technology improving functionality and precision in healthcare tools. This process brings new possibilities to clinical production, focusing on durability, design flexibility, and efficiency.
Enhanced Material Flexibility
Material versatility is one of the benefits of reaction injection molding. Manufacturers can use lightweight polymers and thermosetting plastics to create sturdy products. It is particularly valuable for creating devices with ergonomic designs, like diagnostic equipment or portable monitors.
Additionally, the material properties allow for intricate geometries and thin walls without compromising strength. For example, incubator chambers and custom enclosures for medical imaging machines benefit from the flexibility of RIM. These applications demonstrate how reaction injection molding innovations have expanded functionality in clinical equipment.
Superior Precision and Customization
Another noteworthy aspect is the precision and customization capabilities of RIM. This method supports low-volume production runs without sacrificing accuracy, making it perfect for manufacturing clinical instruments. Since RIM tooling is adaptable, adjustments in design are easy to implement, which supports the development of next-generation equipment.
RIM and low-volume production for medical applications streamline the creation of specific instruments, including surgical handles, brackets, and ergonomic panels. These items require exact measurements and unique design features, and RIM delivers consistently across multiple iterations.
Improved Performance for Clinical Tools
The resilience of parts molded through reaction injection molding ensures longevity, even with constant sterilization and use. For instance, handheld diagnostic tools and respiratory support casings must be durable. Using high-grade polyurethane or composite blends reinforces device durability.
Additionally, using lightweight materials helps clinicians handle devices comfortably. This increases efficiency during long procedures or repeated tasks.
A Future-Driven Manufacturing Approach
Manufacturers are using reaction injection molding to reshape the production of clinical equipment. Lower costs for tooling and materials, combined with advanced customization options, have allowed medical manufacturers to push boundaries in design and practicality.
The growing demand for sustainable healthcare tools reinforces the relevance of RIM in advancing clinical innovations. By enabling more efficient resource usage and improving patient outcomes, RIM continues to provide eco-friendly healthcare solutions.
Would you like to receive similar articles by email?
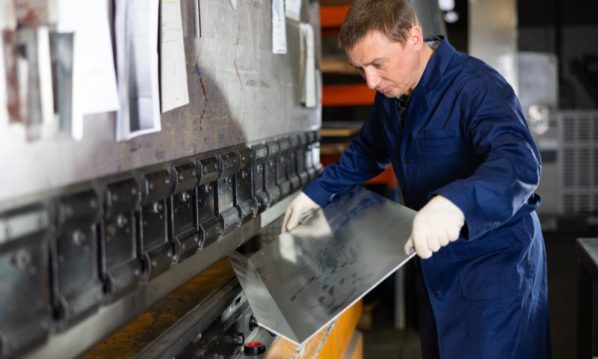
